日本の鍛造業界は屈指の技術で世界をリードしてきています。自動車、重機、電子、建築などいろいろな業界を支えています。
筆者はかつて東京で働いていたのですが、2011年に大阪に引っ越してきて、鍛造関係の仕事を始めました。人生には色々な縁があり、10年以上続いてきた鍛造の仕事は切っても切れない縁を感じています。
冷間鍛造金型の営業マンとして始めた鍛造の仕事は、技術的な内容を理解するのが相当難しいのですね。
理解しにくい難しさには二つの理由があります。
- 金属は金型の中で成形され、目で直接確かめることができない
- “寿命”が一番重視され、関連要素が多すぎ、問題を分析するというより、経験による推測が大事
「石の上にも三年」ですが、「金型」の上にはいくら天才でも精通まで少なくとも5年以上は必要でしょう。
冷間鍛造の金型には色々な種類があり、切断用のカッタやクイル、成形用のパンチやダイス、各種ケース、ピン、フィンガー、ホルダー、スペーサ、ロールなど、私の親友が設計した最も難しかった6段の冷間鍛造の金型は1セットで200枚以上の図面もあります。
営業マンとしての私には、金型の設計は無理に決まっています。
一生懸命に金型の設計を学んでいたことがありますが、概ねに原理と流れを理解できて、計算までの段階にはなかなか登れませんでした。
あるきっかけで、機械に触れるチャンスがあり、二次加工機の「リヘッダー」を販売し、その後、「多段横型鍛造機」いわゆる「フォーマー」の販売を始めました。と同時に、表面処理のメッキラインと熱処理の「連続炉」の立ち上げプロジェクトをコンディネーターとしてリードし、大きな成果を収めました。鍛造業界の上流から下流まで経験し、理解をはるかに深めました。
鍛造の各工程はどちらもとても大事ですが、コアとなっているのはやはり成形です。
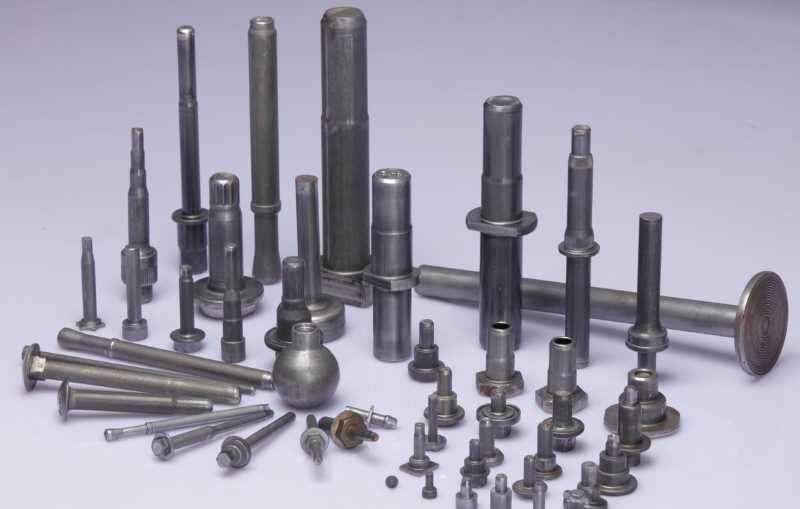
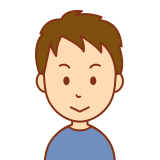
フォーマーの圧造力を利用し、金型の形に金属をたたいて製品を作るのは、実におもしろい仕事です。
それでは、冷間鍛造の仕事を詳しく紹介していきましょう。
鍛造機の分類
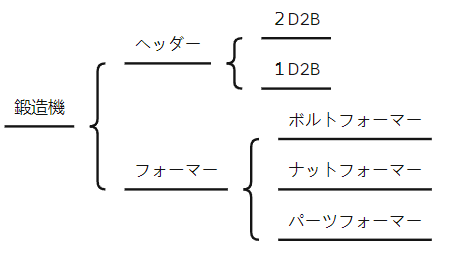
- ヘッダー
- フォーマー
冷間鍛造の主力設備であるフォーマーという種類の機械にはいろいろな種類があります。
一番簡単なのはヘッダーという冷間鍛造機です。ヘッダーの中でも、ダイ2個パンチ2個とダイ1個パンチ2個の2種類あります。2ダイ2パンチは2D2Bと表示され、ヘッダー或いはツーダイツーブローだとよく呼ばれます。1ダイ2パンチはほとんど1D2Bとは表示せず、よくダブルヘッダーだと呼ばれ、たまにはワンダイツーブローだと呼ぶ人もいます。
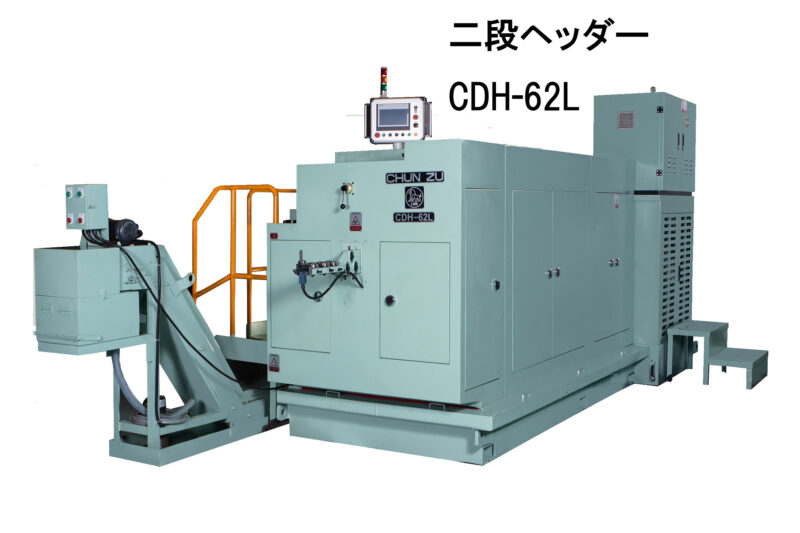
一台の鍛造機にあるダイスとパンチのセット数は「段」だといい、基本的に、ダイスとパンチのセット数が同じで3個以上あれば、「多段」になり、フォーマーだと呼ばれます。例えば、ダイスとパンチがそれぞれ4個あるフォーマーは4段フォーマーになります。
特殊な冷間鍛造機であれば、2D3Bと3D4Bなどもあります。それぞれの特徴があり、そのまま「ツースリー」と「スリーフォー」だと呼ぶことが多いです。
ヘッダーは英語の「Header」で、簡単に言えば、ネジの頭を作る機械という意味です。
フォーマーは同じく、英語の「former」という成形機械の意味です。理解しやすいし、覚えやすいですね。
- ボルトフォーマー
- ナットフォーマー
- パーツフォーマー
製品の種類によって、冷間鍛造機には「ボルトフォーマー」、「ナットフォーマー」、「パーツフォーマー」の三種類あります。さらに細かくすれば「パーツフォーマー」には「ボルトパーツーフォーマー」と「ナットパーツフォーマー」の二種類で分類することができます。
それぞれの違いは何でしょうか?
製品の特徴でフォーマーが違いますよ。
ボルトが長いので、フォーマーのストロークを長くする必要がありますね。
ナットは穴があり、成形しにくいので、フォーマーの段数が多くて、何回もたたいて、金属にたくさんの変形を与えます。ナットが薄いので、フォーマーのストロークはボルトより必要がなくて、ラム往復の距離が短くなり、回転スピードはボルトフォーマーよりはるかに速いのです。
もう一つの違いは、各段の間の伝送方式がワークのつかみ方のところです。ナットフォーマーはワークをつかむ爪は開閉できないのですが、反転ができます。逆にボルトフォーマーのほうは爪の開閉ができますが、ほとんど反転ができません。
開閉はよく「オープン」と言い、反転は「ターン」と言います。「オープン」と「ターン」が同時にできる伝送方式もあり、「ユニバーサル式」と言いますが、まだ珍しいです。
鍛造の技術の発展により、ボルトとナットのような規格品からより複雑な異形パーツになってきて、鍛造機も改良され、パーツフォーマーが誕生しました。
パーツフォーマーの構造はボルトフォーマーやナットフォーマーと同じです。
ナットパーツフォーマーはナットフォーマーよりストロークが長く、ラムの移動距離が長くなり、慣性も大きくなり、長いパーツを作れるだけではなく、より難しい成形も可能になります。
昔のボルトフォーマーは最後の「段」は「トリミング」工程になるのは多いのです。この工程は文字通りで、成形ではなく、ツバや余計のバリとかをカットするのです。今のフォーマーにはほとんどこのような工程がなくて、「トリミング」の工程が必要であれば、ダイスとパンチに工夫をして、トリミングダイスで実現します。なので、このトリミングの段がなくなったので、ボルトフォーマーとボルトパーツーフォーマーの違いもなくなりました。
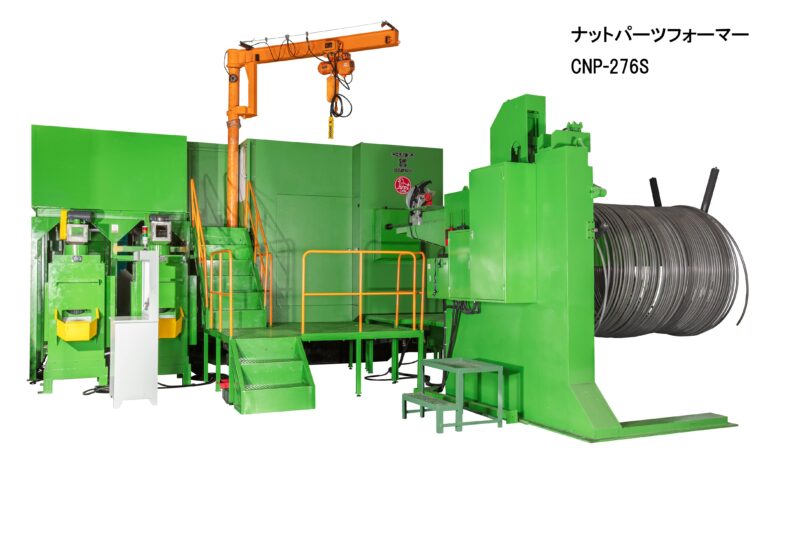
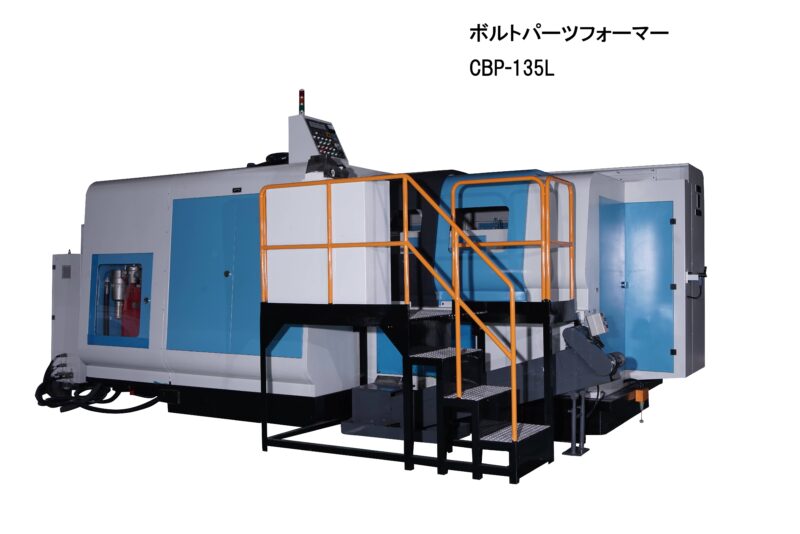
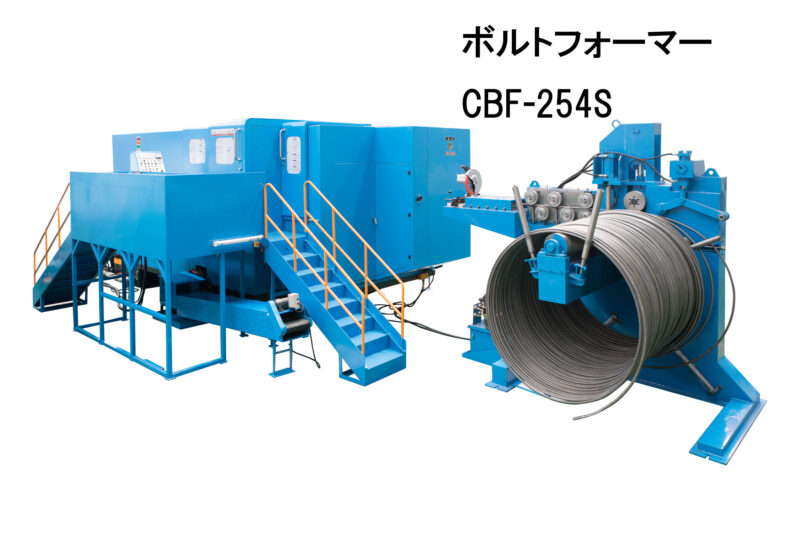
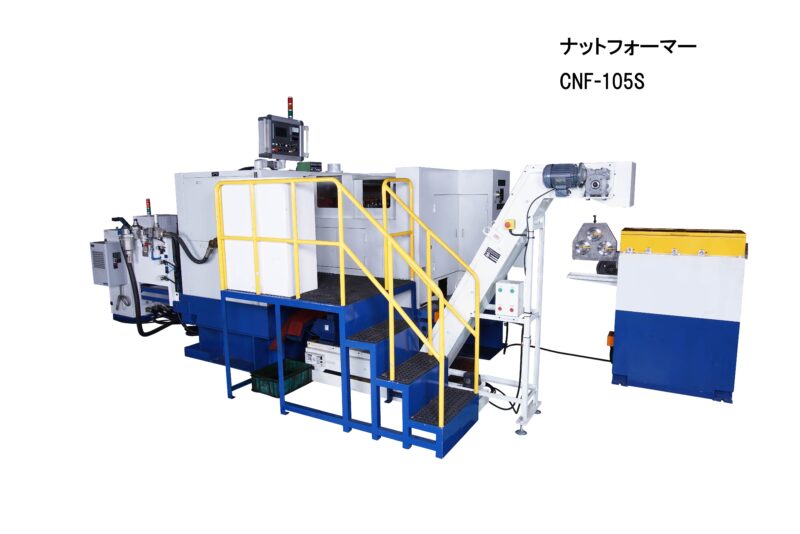
まぁ〜、フォーマーには「ナットフォーマー」、「ボルトフォーマー」と「パーツフォーマー」の3種類があるとおぼえておけば十分です。
鍛造の種類
- 冷間鍛造
- 温間鍛造
- 熱間鍛造
製品を成形するときの温度によって、「冷間鍛造」、「温間鍛造」と「熱間鍛造」の3種類あります。
冷間鍛造とは言え、金属を冷やして成形するのではなく、室温で圧造するわけです。
温間鍛造には決まった温度がありませんが、大体300℃~800℃の間で金属を加熱して成形するのです。厳密に言えば「金属が再結晶温度以下」で、見た目は金属が真っ赤にならない状態で加熱して鍛造する方法です。ステンレスやチタンなどの難加工材を圧造するときによく使う手法です。
熱間鍛造は金属を1000℃以上加熱し、真っ赤の状態で鍛造する方法です。金属がだいぶ柔らかくなって成形しやすいと同時に、焼き入れもできてしまいます。
この三種類の鍛造方法で使う機械はそれぞれ「冷間鍛造機」、「温間鍛造機」と「熱間鍛造機」と言います。
冷間鍛造機に外付けで加熱器を設置し、簡易的な温間鍛造機を使用しているお客さんもいますが、使用温度が高く、潤滑油が漏れて燃えてしまったと聞いたことがあります。安全第一で、くれぐれも注意する必要がありますね。
鍛造機の内容はとりあえずここまでしましょう。まず金型の話をしてから、鍛造機の内容を展開します。
金型
冷間鍛造の手法は据込み、前方押し出し、後方押し出し、密閉、打ち抜きなどあります。これらの手法の組み合わせでいろいろな形の製品ができます。これらを実現するのはダイスとパンチです。
ダイスは鍛造機のダイスホルダーに装着して動かなくて、鍛造後の製品外部形状はダイスに加工してある穴の形状になります。
パンチは鍛造機のラムにあるパンチホルダーに装着し、ラムの往復運動でパンチがワークをダイスの穴に突っ込んだり、引き抜いたり、サイクルします。鍛造後の製品内部形状はパンチの形状になります。
鍛造されたあと、ワークの形状はパンチダイスと同じようになりますね。この過程は金型の形状を金属に転写するといいます。
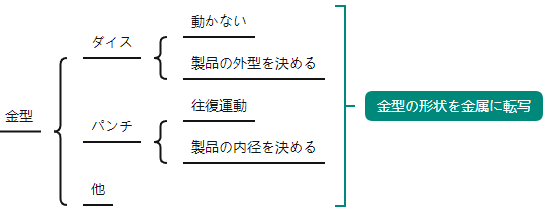
欲しい製品の形状は鍛造で金型から転写されるので、あらかじめ製品の形状を金型に加工しますね。
さて、お客さんから量産品図面をいただいたら、どのように金型を設計するのでしょうか。
実は、金型を設計する前に、「工程設計」をまず考えないといけないです。
工程設計
「工程設計」とは、私の理解では、完成品の最終形状になるまで、ご使用の鍛造設備など実際の制限条件に合わせて、以下の二つの問題を解決することです。
- 「素材を何回打つか」
- 「毎回の途中形状がどのようにするか」
金属が一回で変形できる量は限界があり、限界の範囲にはMinとMaxがあります。
限界のMin以下では弾性変形の領域で、圧力を与えた後に、金属の素材が変形から元の形に戻ります。
限界のMax以上であれば、金属の組織が破壊されてしまうので、素材がごみになってしまいます。
MinとMaxの間は鍛造の仕事の領域で、「塑性加工」ということです。
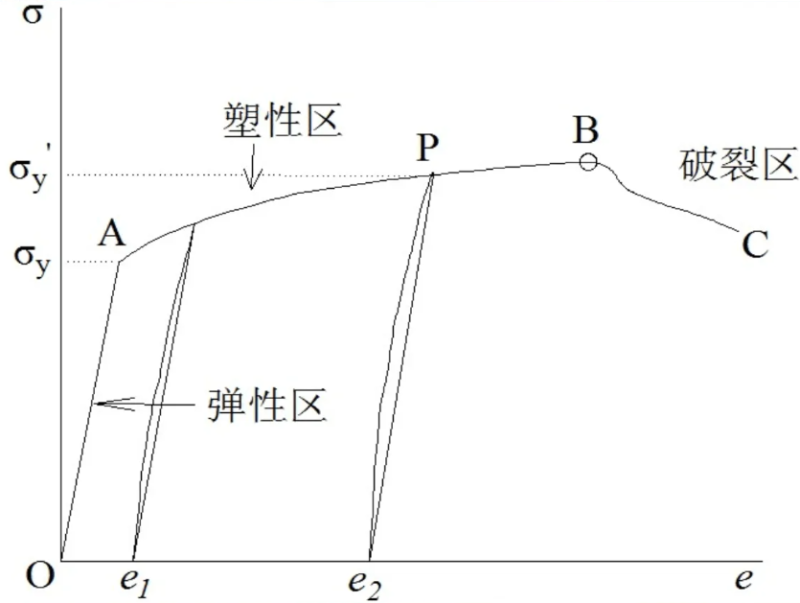
「塑性加工」を簡単に理解すれば、金型の形状を安定的に素材に転写する鍛造のことです。
冷間鍛造では、塑性加工できる範囲が温間と熱間と比べると狭いです。素材から一気に最終形状に圧造できるのは少ないので、何回か打って最終形状に近づいていきます。
毎回の途中形状を決めることは「レイアウトを設計する」とも呼ばれます。
打つ回数分にダイスとパンチが必要で、ダイスとパンチのセット数は「段」だと呼ばれるのはまだ覚えているでしょうか。「何段で最終形状が実現できるか」の設計により、フォーマー選定の一つ重要な基準になります。
段数を増やせば増やすほど、各段の負荷が平均的に減っていき、段数が多い方がいいのではないかと思う人がたくさんいるかも知れません。
しかし実際には、塑性加工範囲の中で、金型の寿命を確保する上で、必要最小限の段数が望まれます。何故なのでしょうか?主に三つの理由があります。
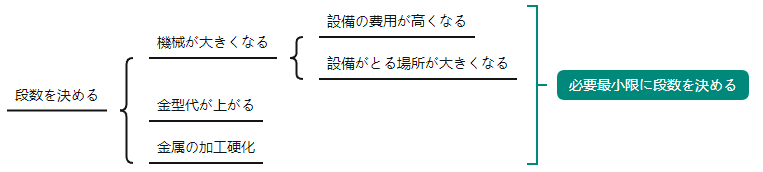
- 段数が増えるとフォーマーが大きくなります。フォーマーには「剛性」という非常に重要な属性があります。いいフォーマーでは必ず剛性がいいのです。この剛性を実現するために、設備メーカーがフォーマーを全体的に考慮し設計しないといけないので、剛性の良い材料を使ったり、部品を太く厚くして大きくしたりするのはよく使われる手法です。1段を増やすと、フォーマーが比例に大きくなるのではなく、極端に大きくなるのです。次第にフォーマーがとる場所は大きくなるし、金額もだいぶ高くなります。しかもフォーマーが大きくなるにつれて、メンテナンスも難しくなり、エネルギがたくさん消耗し、予想外の費用も発生する恐れがあります。
- 段数が増えた分の金型は必要になり、金型代が上がります。鍛造品に含まれる各種のコストには材料代が一番高いのですが、その次に金型代になります。金型代の節約は製品のコストを大きく左右します。
- 金属が鍛造される度にファイバーフローが緊密になり、硬くなります。冷間鍛造では金属を加熱しないので、室温の条件で打てば打つほど硬くなる金属の性質は「加工硬化」と呼びます。段数を増やすだけで、金属が打ちにくくなり、変形しなくなりますので、成形に役立たなくて、無駄がいっぱい生じます。ファイバーフローに触れましたが、後で詳しく説明します。
この三つの理由を念頭に置いて、打つ回数を決めたら、問題2の途中形状を設計することになります。
途中形状
同じ最終形状でも各段の途中形状はいろいろな形が可能で、設計者にはたくさんの知識と経験が当然必要ですし、ある程度の想像力も必要だと私が思っています。
各段の途中形状を変えると、素材変形の量が変わります。変形量と荷重及び使用するエネルギーが比例していますので、鍛造に使う荷重は変わってきます。できるだけ各段の荷重を均等に配分することは工程設計のとても重要なポイントです。
ある段に荷重が集中してしまったら、どうなるでしょうか。
- その段の金型寿命が悪くなります。金型が高い負荷を受けるので、破損が早くなるのも当然ですね。
- ある段の荷重が極端に大きく、フォーマーの力を超えてしまったら、パンチがダイスの中から抜けなくなります。この現象は「ドン付き」と呼ばれています。「ドン付き」は非常に厄介なことで、発生から復旧まで手間も時間も非常にかかります。現場に嫌がられているので、十分要注意です。
- 荷重が偏ってしまったら、フォーマーにもダメージが大きいです。特に長い時間に同じ製品をずっと生産する場合は、フォーマー本体の歪みが発生する恐れがあり、フォーマーの精度が落ちて、メンテナンスやオーバーホールの時期が早まります。
「ドン付き」は本当に厄介です。私が何回も経験しました。
ある製品は5段で鍛造しています。4段目は真ん中の穴を開ける「ピアシング」の工程になります。特別な理由があり、打ち抜くカスが厚くて、4段目の荷重が大きいので、試作の時に何回もドン付きになりました。
ドン付きになれば、フォーマーは完全に動かなくて、フリーズというか死んだような感じです。
特に一回目のドン付きは理由がわからなかったので、ただ突然フォーマーが急停止になって、何をしても動かなくて、壊れたかとすごく怖かったのです。
パンチはダイスの中から抜けなくなって、外では見られないのです。目で確認できないため、停止に至るあらゆる問題を全体的に確認し、やっとドン付きが起きたと判明できました。
復旧するには、まずフォーマーをシャットダウンし、機械カバーを外し、フライホイルに予め設けた穴にバールを入れて、天井クレーンでバールを動かします。レバレッジの原理でフライホイルが逆転し、ラムを後ろ方向に動かし、やっとパンチをダイスから引き抜いて、フォーマーが再び動くようになりました。
これはまだ比較的に小さいフォーマーだったので、もし大型のフォーマーがドン付きになったら、復旧は相当大変ですよ。
最終形状
「ニアネットシェープ」と「ネットシェープ」、この二つの言葉はお聞きになったことがあるでしょうか。
「ネットシェープ」というのは最終的な製品の形状になります。
「ニアネットシェープ」というのは、製品の最終形状に近い状態の意味です。
ピン角や精度の厳しい形状など存在しているので、塑性加工に「ネットシェープ」までできないのがあります。または、無理やり鍛造で完全なネットシェープにするのは金型の寿命が大変悪くなり、型費が増え、費用対効果が悪くなります。
それで、「ニアネットシェープ」まで鍛造で製造して、その後、切削などの二次加工で「ネットシェープ」を完成するのはよくなります。
しかし、鍛造と比べると非効率な切削工程を追加すると、コスト的によくないので、エンジニアたちは知恵を絞って、なるべく鍛造だけで「ネットシェープ」を実現できるように金型を設計しています。
金型によく使う超硬、ハイス鋼、ダイス鋼などの材料を改良し、入念に磨いて、コーティングもかけて、いろいろな工夫をされています。但し、試作の段階で金型を作って、繰り返しテストするのは、一発で成功できればいいのですが、設計を変更するたびに、新しい金型を作らないといけないのですね。たくさんお金を使うし、時間的にも待てなくなります。なので、近年シミュレーションのソフトウェアを使って試作を模擬することが多くなってきています。ソフトを使ってパソコン上で、どこに一番負荷がかかっているのか、製品のファイバーフローはどのように流れているのか、ある程度工程設計の内容を検証できるようになっています。ソフトウェアのシミュレーションは100%実際を再現することがまだできていないのですが、試作の時間とコストをだいぶ節約することができています。しかし有力なシミュレーションソフトは何千万円もするものがあるので、かなりの初期投資が必要ですね。
先ほど「ファイバーフロー」をもう一度言いましたね。ここで詳しく説明します。
ファイバーは繊維で、フローは流れの英語ですね。
金属の組織が形成されている繊維状のファイバーフローは、圧力を加えられて、金型の形状に沿って充満するようになります。工程設計では、如何にファイバーフローを滑らかに流れてもらうようにするかによって、製品の品質を確保するのです。ファイバーフローの流れがきれいになればなるほど、金属の組織が緻密になり、強度が上がります。切削加工は金属のファイバーフローを切ってしまいますので、切削加工より鍛造の方は製品品質がいい一つの理由になります。
塑性加工の領域を超えて、金属の破壊まで圧力を素材に加えたら、実はファイバーフローが異常になってしまったという結果です。ファイバーフローが切れてしまうと金属が降伏点を超えたと言います。
ファイバーフローはよく「ニク」とも言います。意味は多少違いますが、現場の方々に「ニク」だと伝えたら、もっと分かりやすく会話もスムーズになるかもしれません。
体積計算
ファイバーフローがフォーマーの荷重により金型の中で流れて、金型に充満しないと、きれいに金型の形になりません。製品の体積、素材の体積、金型成形空間(キャビティ)の体積は精密に計算しないといけないです。
体積の計算はアナログの計算方法を使っている方もいます。複雑な形状を計算可能な基本形状に分割し、リングや円柱、長方形など別々に計算し、最後の合計は製品の体積になります。
三次元CADの普及のおかげで、3Dデータを作って、3Dソフトは勝手に体積を教えてくれます。材質をソフトに入力すると重量も教えてくれます。とても正確に計算されています。
計算の結果として完成品の体積だということはまず決まっています。
工程設計の中に、「穴抜き」や「トリミング」のような「ニク」が減る工程があれば、その減った分の体積を足して、素材の体積になります。
金型のキャビティの体積は少し複雑になります。
例えば、据込みのような拘束がない工法はキャビティの体積が製品より小さいです。
密閉鍛造であれば、キャビティの体積は製品と同じでないといけないですね。
キャビティの体積が製品より大きかったら、「ニク」が充満されなくて、きれいな形ができないです。
逆にキャビティの体積が製品より小さかったら、余った「ニク」は逃げるところがなくて、金型の破損になり、爆発の可能性もあり、非常に危ないのです。
でも、キャビティの体積は製品の体積とぴったり一致する場合はうまく行くのでしょうか?
素材が金型に入るときに、冷却の油や空気も一緒に入ってしまいます。しかも、高速ですし、密閉状態で圧縮されていき、爆発します。
これもとても危険なので、金型にエア穴や、油溝など付けるように施されて、空気と油が金型から逃げるように工夫されています。
エア穴や油溝が大きかったら、「ニク」も入ってしまって、バリになります。穴と溝の大きさを注意しないといけないし、作るところも考えないといけないです。
もし応力集中しやすい角につける場合は、エア穴から割れやすくなりますので、寿命が悪くなります。
金型の体積がぎりぎりまで設計するのは決していい設計とは言えないです。
「ニク」の「ニゲ」を設けたり、金型寿命が悪い箇所に余裕を持たせたり、負荷の高い密閉を避けたりして、完璧な「ネットシェープ」を求めずに、費用対効果のバランスを持った「ニアネットシェープ」などは経験のある設計者のノウハウです。
試作段階
以上の準備ができてから、各工程(フォーマーの各段)の製品のレイアウトを決めます。つまり問題2「毎回の途中形状がどのようにするか」を設計します。
この部分に入ったら、たくさんの知識が必要になってきます。特に計算が難しくなります。参考できるレイアウトがあり前例のある製品であれば、いいのですが。参考できる例が全くないときには、想像力とロジックと知識の豊富さは設計者に求められて、全面的に物事を考えられる力は大事で、優秀な設計者はナカナカいらっしゃらなくて、とても重宝されています。
いくら優秀な設計者でも、いくらいいシミュレーションのソフトウエアを使っても、設計したレイアウトで一発成功する例は稀でほとんどないです。
普通はver.0のレイアウトで金型を作って1回目の試作をやります。
試作の時に、切断から最後の工程まで各段の工程サンプルを取ります。工程サンプルをレイアウトの設計と比べて設計通りに行っているのかを確認します。
サンプルは設計から乖離が大きい時に、まずフォーマーと金型を調整します。
フォーマーにはダイスの前後調整、パンチの前後と左右調整の機能が必ずあります。パンチの左右調整はダイスとパンチの芯合わせのためです。精度は±0.01mmまで(髪の毛の太さより10分の1以下の精度だと良く言われます)精密に作られている金型ですが、芯合わせは段取り替えの時に油断できない非常に重要な一環です。
ダイスとパンチの前後調整はワークの成形量を調整する機能になります。
試作の時に、「もっと潰して!」「パンチを前に出して!」「ダイスピンをちょっと下げた方がいいなぁ」とかのような指示はよく耳にします。つまり、フォーマーと金型の位置調整によって、金型のキャビティを調整します。キャビティを調整し変形量が変わることによって、調整した段のワークの形状を変更しながらレイアウトを設計変更しています。試作員も金型の位置調整を記録して、例えば「#3パンチは前に1mm出した」「ダイスピンを0.4mm下げた」とか最終製品の完成まで試していきます。
このように金型の位置を調整するだけで済むのであれば、試作が楽になりますが。レイアウトの途中形状がいくら調整してもうまくいかない場合は、ver.1のレイアウトになります。完全にver.0を廃棄する必要がありません、うまくいかないところを設計変更するだけでいいのです。設計変更した金型だけを作って、もう一度試作します。
必要であればver.2もver.3も…、最終製品を完成するまで、同じサイクルを続けていきます。
このサイクルを繰り返すときに、とても頭痛いのは納期ですね!お客様と約束した期限に量産できるようにサンプルを提示しないといけないのですが、一回バージョンアップすると、金型の再製作は時間がかかります。それに、試作時にフォーマーを空けて他の製品が生産できなくなり、試作の回数が多ければ、工場全体の生産効率が落ちてしまいます。注意事項が多いですね。
最初の製品図面から鍛造品としての最終形状を決め、レイアウトを設計し、金型も設計し、試作と設計変更のサイクルを経って、鍛造品の最終形状が出るまでの一連作業は「工程設計」と言います。なので、設計だと名付けていますが、設計だけではなく、内容が豊富ですね。
最後
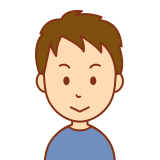
冷間鍛造の仕事に関して、大概な流れでここまで量産前の段階を説明させていただきました。
冷間鍛造の世界は専門的で奥が深いです。内容も多くて、これから紹介していきたいと思います。
コメント