前回は電気亜鉛メッキの前工程を紹介させていただきました。表面処理の種類が大変多いのですが、亜鉛メッキだけではなく、全ての前処理には共通するところがあります。例えばブラスト処理や、ラッピング研磨や超音波洗浄などのような前処理もあり、やり方が全く違いますが、その目的は全て同じで、最も本処理に適している製品の表面状態を整えることになります。
電気亜鉛メッキの本工程
前工程をきちんとこなして、今回は次の本処理から電気亜鉛メッキの最後まで紹介していきます。
筆者が経験した電気亜鉛メッキ設備は電気メッキの槽は全部で12槽があります。メッキ製品が入ったバレルが前処理の中和を終えてから、まず空槽で待機して順番待ちで12槽の電気メッキ槽に入ります。製品を効率よくメッキするために、バレルがメッキ槽に入ってから絶えずに回転します。物理的な回転が電気化学反応を効率良く均一にしますが、あくまで付属的な要因で、主因ではありません。主因は電流の効率になります。
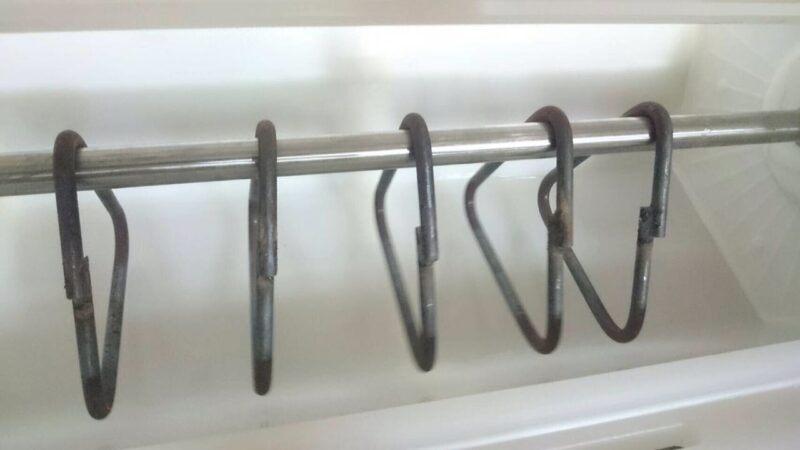
以前も紹介したように、電流の効率がいいので酸性浴を選んだお客さんがネジを作るメーカーです。アルカリ性浴のほうは、膜の均一性が良くて、排水処理も割とやりやすいと聞いていますが、やはり酸性浴の電流効率も生産性も良くて、酸性の塩化浴が選ばれました。アルカリ性浴と比べると膜の均一性が少し劣るかもしれませんが、技術の進歩で薬品と設備の能力が高くなってきて、ネジの精度には十分応えるようになります。環境意識が日々高くなっている昨今、排水処理をきちんと処理しないと絶対ダメなので、これはやりやすいかどうかの問題ではなく、完全に処理しないとならない仕事なので、比較するときに判断の基準にはならないのですね。意思決定の基準になるのはやはりネジという量産品の特徴に合う生産性とコストパフォーマンスなどに限ります。総合的に現状生産に一番相応しいのは酸性の塩化浴になります。
強酸を使う作業なので、酸が蒸発して工場に充満しやすいです。揮発した酸が設備と建屋を腐食しますし、作業者の健康にも悪いです。この問題を解決するには、設備の金属表面や工場の床にFRPの防食塗装を施したり、建屋の換気を良くしたり、作業員がマスクをかけたりすることが多いのですが、効果が限定的です。作業停止している間に、もし酸を使う槽に蓋をしないと、薬品の揮発が速いので、工場の空気が霞んで、数時間で霧に覆われるようになります。
台湾の設備メーカーはこの問題を解決するために、各槽の両側に特別装置を設けて、蒸気を吸収します。バレルを吊るクレーンの上にもカバーを設けて、蒸気を吸い込む装置があります。何十個もある各槽と移動するクレーンから吸い込まれる蒸気を並列のパイプで集めて、最終的に全部スクラバーに吸い込まれて、排気ガスを洗浄システムでちゃんと処理してから工場外に排出します。このエンジニアリングは大絶賛です。この部分の投資は作業者の健康にも環境的に優しくて、設備や建屋のメンテナンスなど、コスト的にも非常に値します。
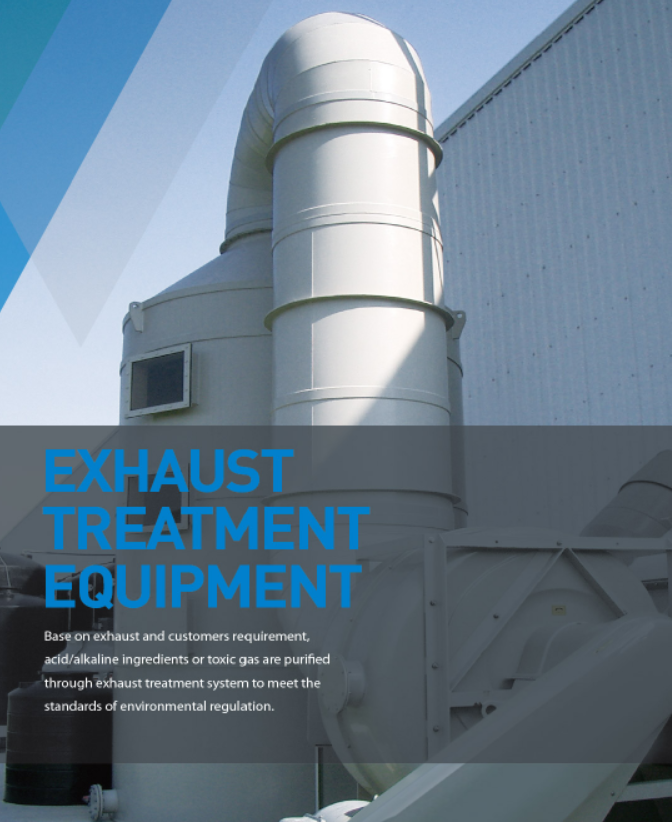
電気亜鉛メッキの原理は、陽極になる亜鉛のインゴットは酸性浴の中に、イオン化になり、陰極の製品(ネジ)の表面で析出して、製品の表面上亜鉛の膜が形成されることです。元々メッキ浴の中に亜鉛のイオンが入っていて、陰極で析出される亜鉛イオンを補充する形で、陽極のインゴットがどんどん溶けていきます。
各メッキ槽に一台ずつ整流器が整備されています。電源からの電気は整流器で制御し、プラスを陽極のインゴットに接続し、マイナスをバレルにつなぎ、陰極である製品(ネジ)に接続します。電流は整流器から陽極に流れ、メッキ浴のイオンを経由して陰極に流れ、陰極から整流器に戻り循環します。整流器では流れている電気の電流と電圧を調整する機能があります。メッキ浴の薬品濃度を安定に保ちながら、電流と電圧及び時間の調整でメッキのスピードを制御し、膜の厚みをコントロールします。
メッキ浴が電気化学反応の環境なので、品質安定なために、薬品濃度は必ず一定の範囲に保ちます。全自動の設備ではベース剤や添加剤の補充を自動で行いますが、定期的にメッキ浴を取り出し、分析しないといけないです。手動の分析になりますが、分析の結果は記録し、メッキ浴の状況確認と変化の傾向が把握できます。分析の結果を統計し、メッキ浴の状態をデータ化することができるようになります。このデータと実際状態を参照しながら、品質向上するためにどのようにメッキ浴を調整するのか、品質問題が起きた時どのように改善するのか、生産に役立つ新しいテクニックとか、このような積み重ねでやがてお客様独自のノウハウになります。例えば、添加剤には光沢を出す薬品があります。多めに光沢剤を入れるとメッキしたネジがピカピカになり、金属の光沢は非常にきれいです。しかし、外観上はすごくよくなりますが、膜が脆くなる傾向があり、製品との密着性が落ちてしまいます。ピカピカのネジを取り出しますと、容器に細かい金属粉末が増えてきます。手でネジを軽く握ると手にもピカピカの金属粉末が付いてしまいます。メッキ不良になるかどうかは剥離される金属粉末の量によりますが、正常の範囲に持っていくために光沢剤の濃度を薄くする必要があります。どのように他の薬品濃度を影響せずに、どれぐらい濃度を下げればいいのか、薬品メーカーの指導とアドバイスを受けながら経験を積んでいき、結局メッキ生産者のノウハウになります。
メッキ浴を管理できれば、生産を制御するのに電気と時間を調整します。設備の生産能力を決めるのは1バレルに入れる製品の量と1サイクルの時間の二要因です。1バレルに入れる製品のMAX量は製品の形状に関連しています。例えば長いネジであれば、同じ空間の中に短いネジより入れる数量は少ないですね。生産能力とは製品の重量で計算されるのは一般的ですが、実は表面処理の生産能力は表面積で計算するのが正確です。同じ重量のネジをバレルに入れても、小さい短いネジであれば総表面積はずいぶん大きいです。
お客様がネジの鍛造メーカーなので、製品の種類は専門のメッキ業者と比べるとかなり少ないのです。というわけで、生産管理の難易度が若干低いのもあり、メッキの生産サイクル時間の設定も管理しやすいです。
管理方法として、一番生産量の多い品種を基準にし、サイクル時間を決めます。そして、サイクル時間を基準にし、各品種の表面積に基づいて電流電圧を設定します。さらに電圧を一定にして電流だけ調整します。このようにすれば、各パラメータのデータをリストにまとめて、調整するのは電流だけなので、一目瞭然で作業者の指導も説明しやすいのです。
なぜメッキ槽は12槽になったのか、その設計はどのような計算になるのでしょうか。
電気亜鉛メッキの本工程は60分が必要です。つまり、既存のメッキ浴では電流効率や製品特徴など全ての条件を纏めて、メッキ槽の中で60分間の電気化学反応が必須だという計算です。
メッキ本工程以外の工程では5分間で循環できます。例えば前処理の酸洗は10分が必要だとすると、5分間に合わせるために酸洗は2槽を設けます。この5分のサイクルで、60分のメッキ時間には12槽が必要になる計算です。
全てのパラメータを調節できるのは設備の柔軟性を誇ることですが、実際の作業に合わせて一番やりやすい方法で、且つ求めている効率と品質が無限に再現できることは自動化設備の評価になり、量産というそのものの意味です。電気亜鉛メッキ設備にとっては、まず薬品メーカーがお客様のリクエストを分析し、メッキの条件を設備メーカーに伝えます。
設備メーカーが薬品メーカーから説明を聞いて、薬品の特性とメッキの条件を十分に理解して、自分の設備を見せかけるのではなく、現場の制限とお客様の作業習慣などを熟慮する上で、実際に役立つ機能を誠実に洗い出し最後の設計を完成します。お客様も自分の立場にも設備メーカーと薬品メーカーの立場にも立って、メッキの内容を徹底的に把握して生産を行うことで、3社共に最大限の協力をし無駄をなくして最後の成果に結びますね。
電気亜鉛メッキのランニングコストといえば、電気代や水代と薬品は消耗品として大きなウェイトを占めてあります。特に薬品に関しては、実際の化学反応に消耗されますが、たくさん汲み出されてしまい、浪費されています。製品やバレルに付着して浪費されて、完全に無くすことが無理ですが、なるべく低減するためにバレルを槽から吊り上げられて、すぐに次の槽に移さず浴液ができるだけ槽に滴れ戻るように、しばらくバレルを吊り上げるままにします。台湾の設備メーカーはさらに吊り上げる頂点に達す時点でバレルを何回か回転させて浴液を効率よく滴れ戻します。この時間を長くすればするほど薬品の浪費が少ないのですが、時間が伸びた分の生産効率も落ちてしまいますね。生産性とコストの両立をバランスよく取るのは設備メーカーの高いレベルの印です。細かいところまで気を配って、全ての動作を5分のサイクルに収めて、全ての工程がタイミング良く連動するのは、現場にいた筆者が生で観察できて、本当に魔法のように見えて、大変感動しました。
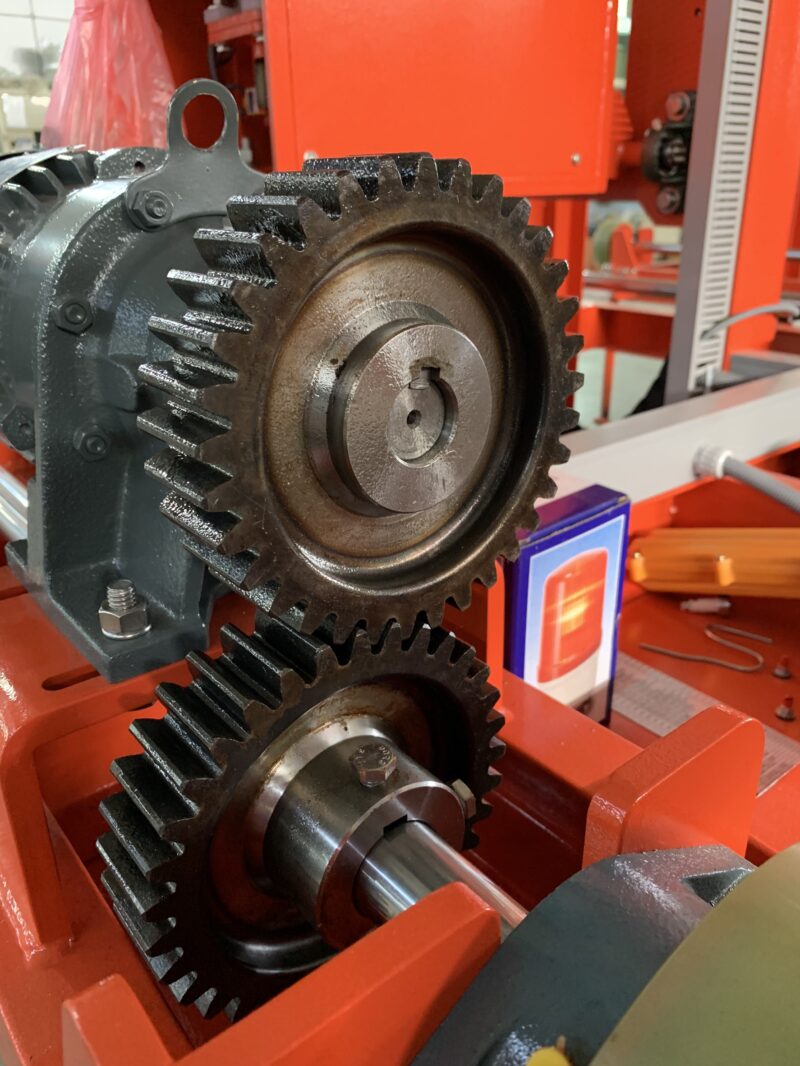
メッキの本工程が終わったら、水洗で浴液をきれいに洗います。とりあえずこれで亜鉛メッキが終わりますが、全体の作業としてはまだ半分の工程しか行っていないのですよ。亜鉛メッキが終わって、バレルから取り出し、メッキ品質の状態を目で確かめます。その後、専用の円柱状のバケツに入れます。ここからバレルが卒業します。残りの作業は全部このバケツで行います。
ベーキング処理
次はベーキング処理します。ベーキング処理する前に、水洗いで残っている水分を完全に乾かさないといけないので、温風遠心脱水機にバケツを丸ごとに投入して脱水します。脱水完了後、きれいな銀色が光っているピカピカの製品をベーキングします。
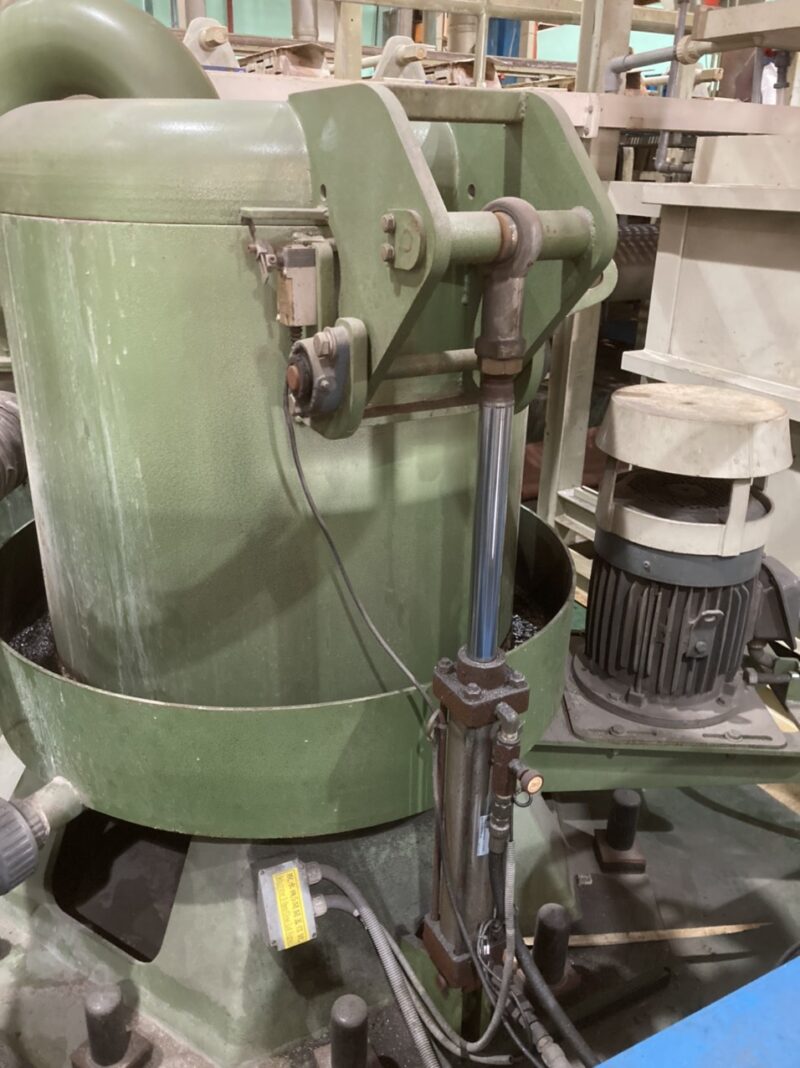
ベーキング処理は以前紹介した水素脆性を解決するための工程です。水素脆性は名前通りに水素の影響により金属がもろくなる現象と指します。金属は粒子の結晶組織の形違いで硬度が変わります。この結晶組織がうまく結合できなければ欠陥が起きてしまい、金属の硬度や靭性が落ちてしまいます。例えば鉄の場合、鉄の粒子と炭素の粒子が色々な形で結晶し違う特性が現れます。このような性質を利用して熱処理をしますね。水素の大きさは炭素の原子と比べても鉄の原子と比べても非常に小さいので、鉄と炭素が結晶している組織に水素が入りやすいわけです。しかも、水素が発生する前工程の酸洗いや電解洗浄やメッキの本工程でも加熱や電気を流しているので、水素が金属の表面から奥までもっと入りやすくなっています。金属に入った水素が鉄と炭素の結晶格子に入ってしまい、欠陥が起きてしまいます。一番厄介なのは、このような欠陥により金属がもろくなりますが、なかなか検査しにくいし、金属が劣化している予兆は全く現れないのです。ある日突然金属が折れてしまうときにはじめて水素脆性が起きていると分かったケースが多いです。
メッキすればほぼ逃げられない問題の一つで水素脆性を解決しないとならないので、水素の発生を抑えることとか、水素が金属に近づくことを避けるとか、方法がいくつかあって、水素脆性を低減するのが可能です。すでに金属に入った水素を追い出すことはもっと大事です。この作業はベーキングだと言います。
ベーキングは「焙じる」「焼く」という意味の英語です。つまりメッキした製品を加熱して、水素を蒸発して取り除く作業になります。熱処理に近いイメージですが、処理条件が違います。熱処理が熱処理炉で行い、バッチ炉というタイプがあり、オーブンのような形です。ベーキングもベーキング専用の炉があり、このバッチ炉に似ています。ベーキング作業は普通180℃~200℃の間で製品を8時間加熱する工程ですが、そこまで水素脆性がひどくない場合は4時間することもあり、必要な場合だと12時間さらに16時間もすることもあると聞いています。皮肉なのは、ベーキングの効果を測る手段はまだ普及していないようで、完全に検査できないらしいです。コストダウンのためにベーキング時間を短縮したり、さらに省略したりするメッキ屋さんもあるようです。もしエンドユーザー様の要求でベーキングしなくてもいいのであれば、無視しますが、コストダウンを理由にベーキングをなくして、万が一金属が折れて大惨事になって後悔するより、きちんとすべての工程を熟すことが大事ですね。
180℃~200℃という温度の範囲で、鉄にとって実に難しい条件です。ご存じかもしれませんが、鉄製品は熱処理して硬度を出して使用しますね。熱処理にも各工程があり、まず焼き入れをして、十分硬度を出して、その後焼き戻しをやります。焼き戻しでは若干硬度を下げますが、十分な靭性を鉄製品に持たせて、硬さと脆さのバランスを調整します。この焼き戻しは高温焼き戻しと低温焼き戻しの二種類があります。合金鋼など高級な鋼材は高温焼き戻しをしますが、普通な鉄鋼や低炭素鋼では一般的に低温焼き戻しをします。低温焼き戻しの温度も200℃前後になります。電気亜鉛メッキのような表面処理は製造工程の中に一番最後になり、熱処理後にメッキ処理します。焼き入れと焼き戻しをしてからちゃんと硬度を出している製品がベーキングの炉に入って、さらに長時間200℃ぐらいの熱を加えたら、もう一度焼き戻しを実施したことになります。この処理によって、製品が柔らかくなり、不良品が出ます。このリスクを避けるために、焼き戻し温度とベーキングの温度を規定範囲の中にうまく調整する必要があります。もし熱処理も表面処理も自社生産ではなく、専門業者に委託するのであれば、事前に処理条件をよく確認してから決めないとだめですね。
ベーキング処理はただ電気亜鉛メッキ後の製品をバケツに入れ替えて電気オーブンのようなベーキング炉に入れて処理を終えるまで待つだけです。ベーキング炉も昇温とキープの循環を全自動で制御しているので、手動作業は製品を「入れる」と「取り出す」の二つだけです。でもベーキングが終わっても表面処理はまだまだ終わっていません。
ベーキングすることによって、処理する前のピカピカ銀色の製品が暗く黒くなります。なぜこのような現象が起きてしまうのでしょうか。実は電気亜鉛メッキの原理は、鉄よりもっと酸化反応しやすい亜鉛を表面に付着することで、鉄の代わりに亜鉛層が先に腐食して鉄を守ることなのです。亜鉛メッキ完成後にベーキングしなくてもただ空気中に置くだけで短時間でピカピカの銀色が暗くなりますし、ベーキング処理が熱を長時間加える作業で、炉自身が密封して加熱しますが、真空ではないので、亜鉛が腐食してしまいます。
クロメート
万全を期するために、亜鉛層も守って防食対策します。この防食対策はクロメート処理だと呼ばれます。
クロメートは化成処理の一種です。亜鉛層の上に、クロム酸塩の膜を形成することで、亜鉛層を酸素や水分と隔離して亜鉛の腐食を防ぎます。装飾のニーズで製品表面が多彩な色も求められます。市場によく出る青色、黄色、黒色などのメッキ品はクロメート処理によって生成されたものが多いのです。
電気亜鉛メッキを処理される場合よく言われることで、六価は毒性があり、日本ではほとんど禁止されており、三価であれば環境にも人間にも優しくて亜鉛メッキの標準になっています。しかし、亜鉛の原子価には六価がないはずですね。実はここの三価と六価というのはクロメート処理のクロムの原子価になります。六価は毒性があるとは言っても、防食性が良くて、環境問題の厳しいヨーロッパの国では逆に採用されていると聞いています。どれにしても、クロメート処理には重金属汚染物質が出るのは間違いがないので、必ずきちんと排水処理をしないとだめです。
クロメート処理は製品を専用の薬品に浸漬するだけ膜が形成されますが、膜形成の効率を高めるためにクロメートする前に、ベーキング後の製品をよく水洗いしてからまず軽く硝酸で活性化します。そしてクロメートの槽に入れるとバケツの揺動と回転で薬品を撹拌しているようなイメージで化学反応させて、さらにバブリング装置を付けます。バブリングとは浴に空気を送り込んで、気泡をいっぱい出します。泡の力で浴を流動するようにして反応効率を上げます。
電気亜鉛メッキの槽もクロメートの槽も正確に薬品の濃度をコントロールする必要もあり、水道水の中の不純物が化学反応の邪魔をしますので、純水を使います。純水を作る装置も高価で、大切な設備です。
トップコート
クロメートが終わってもトップコートという工程がまだ残っています。海外だと「sealing」という表現を使われています。つまり亜鉛メッキ層の上にあるクロメート層にさらに封止膜をつけることで、万全な防錆対策を取ります。
トップコートが最後の工程になりますが、その後良く洗って熱風遠心脱水機で乾燥脱水して電気亜鉛メッキの表面処理作業が完成します。
実は、ベーキングの一番合理的な順番として、最後の工程にした方がいいのです。
しかし熱を加える為、ベーキング後に見栄えがどうしても暗くなります。水素がよく出る工程が前工程と電気亜鉛メッキの本工程で、クロメート以降の工程で水素の出る量は限定的です。綺麗な見栄えを確保するために、電気亜鉛メッキ後にベーキングし、その後にクロメートするのもよくあり、水素脆性には問題がなく、製品品質にも問題がありません。
これで一応一通りに電気亜鉛メッキという表面処理の工程を紹介しました。如何でしょうか、少しでもお役に立ったのでしょうか。
コメント